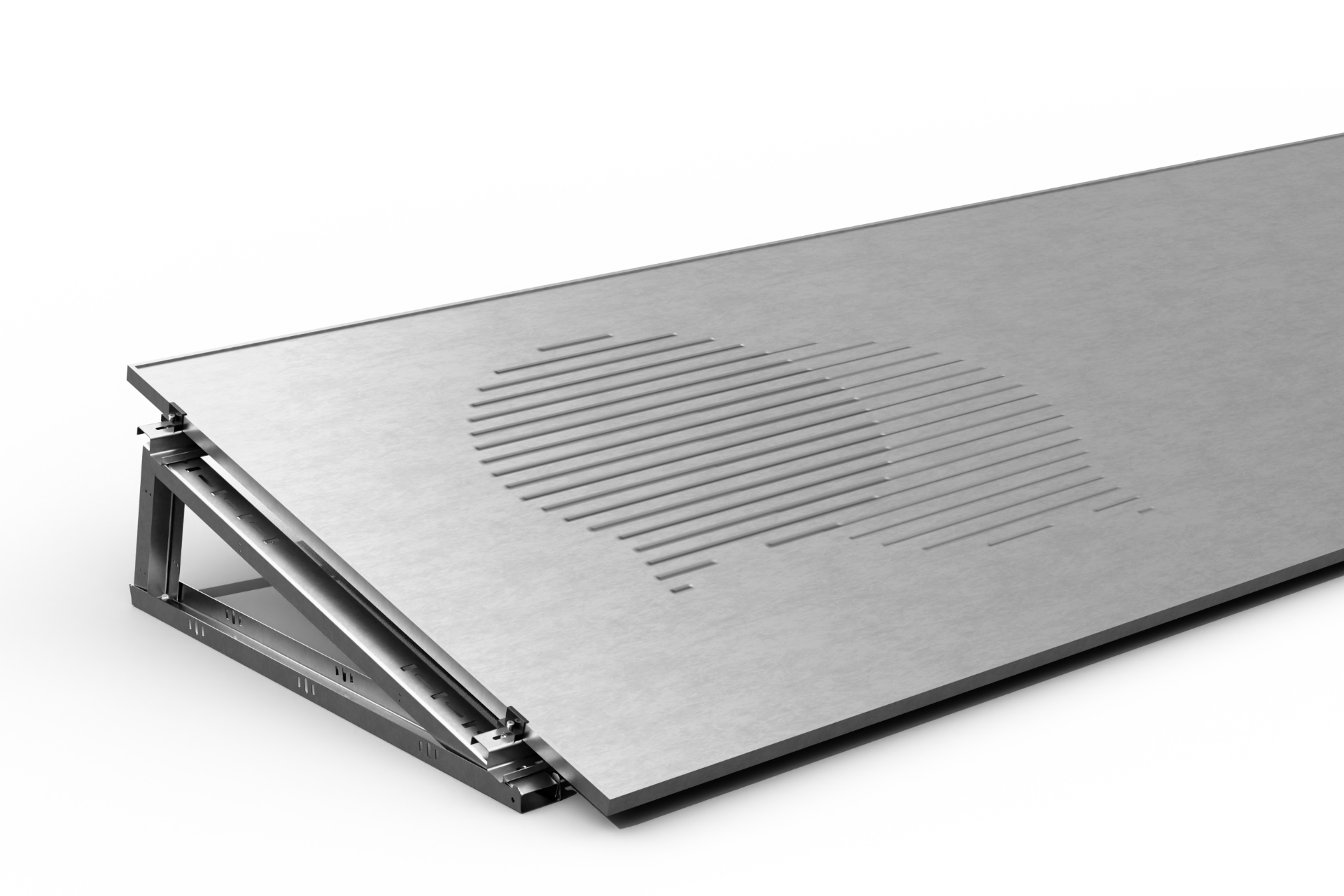
FAQ
PG Group has gone through all the steps needed to meet the ISO 14001 environmental standard and is certified. To obtain the ISO 14001 environmental standard, the company had to meet the following conditions:
Implementation of an Environmental Management System (EMS).
- Conduct a preliminary audit to assess the current state of the organization.
- Develop and implement a documented EMS system, including:
- Environmental policy
- System procedures
- Operational instructions
- Identification and evaluation of environmental aspects related to company operations.
- Identify environmental goals and objectives in line with company policy.
- Ensure compliance with applicable environmental laws and regulations.
Operation of the system
- Ensure management commitment to building and maintaining the EMS.
- Implement a process approach and PDCA (Plan-Do-Check-Act) cycle.
- Conduct monitoring and measurement of key environmental parameters.
- Training of employees on ISO 14001 requirements and implemented procedures.
- Implement operational controls for processes related to significant environmental aspects.
- Develop and implement emergency response procedures.
Certification
- Conduct an internal audit to verify compliance with the requirements of the standard.
- Take corrective and preventive actions when non-compliance is detected.
- Pass a certification audit conducted by an accredited certification body.
PG Group complies with EN 1090 and is certified The company had to go through the following stages:
Implementation of the Factory Production Control System (ZKP).
- Develop and implement a documented system of Factory Production Control (FPC).
- The ZKP system should cover all special processes used in production, such as:
- Design (if the company conducts such a process)
- Welding
- Corrosion protection
- Joining with mechanical fasteners
- Inspection and testing
- Provide adequate personnel, equipment and procedures to ensure product compliance.
Meeting technical requirements
- Meet the technical requirements of EN 1090-2 for steel structures or EN 1090-3 for aluminum structures.
- Conduct the first type test (ITT) and first type calculation (ITC) for products.
- Welding quality assurance according to ISO 3834 (part 2, 3 or 4).
Certification
- Passed initial inspection of factory production control by an accredited notified body.
- Successful completion of a certification audit covering the full scope of the ZKP system.
- Obtain a certificate for the Factory Production Control system and a Certificate for Welding.
Additional requirements
- Having qualified personnel, including welders with the appropriate licenses.
- Provide appropriate equipment for production, measurement and inspection.
- Implement a system for overseeing documentation and records.
- Development and application of product conformity assessment procedures.
The current EN 1090 certificate of conformity is valid until 12/12/2026.
Sheet metal perforation is the process of creating regular holes in metal sheets, which can have different shapes, sizes and patterns. These holes are usually arranged in a predetermined pattern (e.g., in rows, passing or otherwise). Perforation is performed to give sheet metal certain functional, aesthetic or technological properties.
Perforation features:
- Shape of holes: Round, square, rectangular, hexagonal, decorative (such as irregular patterns).
- Arrangement of holes: Regular (symmetrical) or irregular, in straight or staggered rows.
- Size of holes: From very small (e.g., less than 1 mm) to large (several centimeters).
- Degree of perforation: Percentage of perforated area in the total area of the sheet.
Sheet metal perforation methods:
- Mechanical (perforation press):
- The most widely used method in the industry, using dies and stamps.
- Laser:
- It allows precise cutting of any design, especially in custom production.
- Hydro cutting (hydro cutting):
- Used for complex shapes and materials that are difficult to work with.
- Chemical (digestion):
- Mainly used for thin sheets and delicate designs.
Applications of perforated metal sheets:
- Ventilation and permeability:
- In ventilation, air conditioning and filtration systems.
- Design and Architecture:
- Building facades, acoustic screens, suspended ceilings, balustrades, decorative elements.
- Industry and Technology:
- Screens in machines, guards, work platforms, acoustic panels.
- Protective applications:
- Security grating, machine guards, burglar protection.
- Agriculture and food industry:
- Machine components for sorting, drying or processing products.
Thanks to perforation, sheet metal can combine lightness with strength and functionality, making it an extremely versatile material.
In our offer we have welding services by various methods. Depending on the customer’s needs, we are able to offer welding by methods: TIG, MIG/MAG and electrode welding.
MaksyThe maximum thickness of laser cutting depends on the type of material:
- Stainless steel: 30 mm
- Carbon steel: 25 mm
- Aluminum: 25 mm
- Copper: 15 mm
These values are achievable on the TruLaser 3060, which offers the greatest cutting capabilities of the machines listed.
For sheet metal with a thickness of 2 mm, the maximum bending length is 8300 mm. This is possible on the VarioPress 300-80, which has a maximum bending length of 8300 mm and can handle materials up to 4.0 mm thick.
Galvanized sheet and zinc-magnesium coated sheet differ in several important features:
Coating composition
- Galvanized sheet: It is covered with a layer of pure zinc.
- Zinc-Magnesium Sheet: The coating consists of zinc with magnesium added, which provides better protective properties.
Corrosion resistance
- Galvanized sheet metal: Provides good protection against corrosion, but is susceptible to coating damage during transportation and installation.
- Zinc-magnesium sheet: It has much better corrosion resistance than galvanized sheet.
Durability
- Galvanized sheet: It has a shorter service life compared to zinc-magnesium sheet.
- Zinc-magnesium sheet: It is characterized by longer life and better protection of the steel substrate.
Thickness and weight of the coating
- Galvanized sheet metal: Requires a thicker coating for adequate protection.
- Zinc-Magnesium Sheet: Achieves comparable or better protective properties with less coating thickness and weight.
Resistance to weathering Zinc-magnesium sheet shows better resistance to salt spray, moisture and sulfur dioxide compared to galvanized sheet.
The completion date is determined by a number of factors, such as the complexity of the project, technological complexity, production volume and the current production plan of the plant. Each project is treated individually. The time can vary significantly and range from 1 to 4 weeks.
When it comes to the service business of our manufacturing plant in Nowa Wies Wroclawska, we focus on B2B cooperation. We cooperate with a wide range of companies from micro-enterprises to major global corporations. We do not have a set MOQ, but everything depends on the individual project.
Delivery time depends on whether it is an individual “tailor-made” project, or it is a standard order, the components of which are in stock. In the case of a standard design order, the time is limited only to the order reprocessing time and shipping time. For large individual projects, the lead time is usually several weeks, depending on the degree of preparation of the necessary information by the customer.
coated with zinc-magnesium anti-corrosion coatings, e.g. Magnelis or POSMAC
As a standard, the structures are made of S350GD structural steel. This is a metallic-coated variety, which is characterized by high strength and corrosion resistance.
Mechanical properties
- Yield strength (Re): ≥350 MPa
- Tensile strength (Rm): ≥420 MPa
- Elongation at break (A80): ≥16% (for thickness of 0.7-6 mm)
The angle of the structure depends on the selected design. It usually ranges from a dozen to several dozen degrees. It depends on the type of structure and its configuration. The angles can be fixed or adjustable.
Each installation requires an individual assessment before implementation, in particular determining the maximum load on the roof, the actual condition of the roof and its sheathing, and an analysis of wind force and snow load. Only after a full analysis is performed are we able to determine whether a particular roof is suitable for photovoltaic installation.
A system that is welded to a bitumen membrane or roofing felt.
- Palowanie
- Betonowanie
- Przykręcanie do balastu
- Regularne przeglądy: Przeprowadzanie regularnych kontroli technicznych instalacji.
- Czyszczenie paneli: Usuwanie zanieczyszczeń z powierzchni paneli, takich jak kurz, liście czy śnieg.
- Monitorowanie wydajności: Śledzenie wydajności systemu, aby wykryć ewentualne problemy i zoptymalizować produkcję energii.
- Roof strength: The roof must be able to withstand the additional weight of the panels and structure.
- Slope angle: The roof should have an appropriate pitch angle for optimal use of solar energy.
- No shading: The roof should be free from shading by other parts of the building, trees or other obstacles.
- Stable foundations: The structure must be stable to withstand weather conditions such as wind and precipitation.
- Sufficient space: Sufficient space must be provided on the plot to accommodate the panels.
- No shading: The area should be free from shading by trees or buildings to maximize solar radiation.
- Space saving: Installation on the roof does not take up additional space on the plot.
- Less risk of theft: Panels on the roof are harder to steal than those on the ground.
- Enhanced aesthetics: the panels can be discreetly installed and less visible from ground level.
- Better ventilation: panels mounted on the ground have better ventilation, which can increase their efficiency.
- Setup flexibility: Ability to position panels at the optimal angle and direction.
- Easier maintenance access: Greater accessibility to panels makes maintenance and repairs easier.
Roof structures are mounting systems used to install photovoltaic panels on the roofs of buildings. These structures are adapted to different types of roofs, such as flat, pitched or tin roofs.
Ground structures are mounting systems used to install photovoltaic panels in open spaces such as fields or wastelands. They are stabilized with concrete foundations or earth bolts.
A photovoltaic system, designed and built by an experienced company using panels, inverters, electrical accessories and high-quality solar cables, is a very safe electrical device. The risk of electrocution or fire is most often due to errors in design or installation. The fire safety regulations. amended on August 19, 2020 have increased restrictions, reducing the risk of improper installation. Under the new regulations, any installation of more than 6.5 kWp requires a design agreement with a fire protection expert and notification of the State Fire Service.
In order for a properly designed and installed photovoltaic system to operate trouble-free for 25-30 years, the right choices must be made. The right choice of an installer and photovoltaic components of the highest quality, from a proven wholesaler, guarantees many years of installation efficiency and high savings on electricity.
Before setting up photovoltaics on your home, business building or farm, it’s a good idea:
- Verify the credibility and reputation of the installation company: a reputable company will prepare the installation with attention to all details and in accordance with standards.
- Make sure of references: it’s a good idea to check the latest photos of projects to make sure the installer has professional installation crews.
- Choose a professional supplier of photovoltaic and electrical components: before buying, it is worthwhile to analyze the offer of a photovoltaic wholesaler, check the offered models of panels, inverters and PV security systems. It is important that the components have certificates of compliance with the European standard.
- Ensure full and professional after-sales care: this is a guarantee that in the event of a breakdown, you will receive the technical and service support you need, and your request will be handled quickly.
With these steps, you can be sure that your photovoltaic installation will work efficiently and bring the expected savings.
Photovoltaic structures dedicated to monofacial and bifacial panels differ in several key aspects:
- Mounting method
Structures for monofacial panels: Can be mounted directly on the surface of the roof or ground, with no need for light access from below.
Structures for bifacial panels: Require special mounting that allows light access to both sides of the panel. They are often installed on elevated structures, for example. - Substrate materials
For monofacial panels: The type of substrate has no significant effect on performance. For bifacial panels: A highly reflective substrate, such as white paint or concrete, is required to increase the efficiency of the panels. - Tilt angle and orientation
Monofacial panels: Usually mounted at an optimal angle toward the south. Bifacial panels: Can be oriented vertically east-west or standard south-facing. - Use of space
Monofacial panels: Require more surface area to achieve the same output.
Bifacial panels: Allow for better space utilization due to higher output per unit area.
Cold-formed profiles are widely used in many areas of industry and construction:
1. steel structures:
- Skeletons of buildings: Warehouses, industrial halls, commercial buildings, sports facilities.
- Roof structures: Roof trusses, purlins, rafters, support members.
- Partition walls: In lightweight construction, such as in drywall systems (C and U profiles).
- Temporary structures: Storage tents, scaffolding, construction barracks.
2 Housing:
- Frame houses: Cold-formed profiles are used as load-bearing elements in lightweight steel construction.
- Roof cladding: Support for trapezoidal sheets, sandwich panels or other roofing materials.
- Ceilings and attics: As support elements in the construction of wooden ceilings and utility attics.
3. transportation infrastructure:
- Bridge structures: Reinforcing and structural elements of bridges.
- Safety barrier components: Profiles used in road and rail barriers.
4 Industry and logistics:
- Storage shelving: lightweight and durable steel shelving components.
- Construction of industrial equipment: Machine housings and framework.
- Containers and steel packaging: Supporting structures for shipping containers.
5 Energy and photovoltaics:
- Support structures: Racks for photovoltaic panels and solar power systems.
- Towers and masts: Structural elements of power poles and communication masts.
6 Architectural applications:
- Building facades: Profiles as substructure for facade panels.
- Bus shelters and canopies: Lightweight structures for bus shelters, terrace canopies or parking lots.
7 Agriculture:
- Construction of agricultural facilities: Halls, sheds for agricultural machinery, barns.
- Silos and tanks: Structural components of grain or feed tanks.
Cold-formed profiles are popular for their versatility and adaptability to specific project requirements.
Cold-formed profiles are characterized by high strength, which is one of their key advantages. Here is the most important information on the strength of cold-formed profiles:
- High bending, tensile and compressive strength
- High structural rigidity with relatively low weight
- Resistance to mechanical and chemical damage
The strength of cold-formed profiles can vary depending on their dimensions and shape. For example, the bending strength for different hollow sections can be:
- 50x50x5 mm profile: approximately 45 kN
- Profile 80x80x6 mm: about 72 kN
- Profile 100x100x8 mm: approximately 117 kN
- Profile 120x120x10 mm: approximately 180 kN
Cold-formed profiles are structural elements produced by cold bending sheet metal, which makes it possible to obtain shapes such as channels, zetches, angles, T-sections or omegas. Due to their strength, lightness and ease of installation, they are widely used in many areas of construction and industry.
Yes, perforated facade coffers are one of the available finishing options that offer additional aesthetic and functional benefits. Perforation of facade coffers involves making holes in them through a punching or laser cutting process.
Advantages of perforated facade coffers
- Aesthetics: Perforation allows the creation of unique patterns and visual effects on the building facade.
- Light control: openings in the coffers allow partial light to pass through, which can be used to create interesting lighting effects.
- Ventilation: Perforation can improve air circulation in a ventilated façade system.
- Acoustics: Perforated coffers can contribute to better sound insulation in a building.
- Lightweight construction: Perforation reduces the weight of the coffers, which can be beneficial in some projects.
Sheet perforation is the process of making holes of a specific shape and arrangement in sheets of metal. It is a technique widely used in industry and construction, offering many functional and aesthetic benefits.
Flashings are made of different materials and in different thicknesses, depending on the application and project requirements. The most commonly used thicknesses are:
- Coated steel (galvanized with a coat of paint):
- Thickness: 0.5 mm – 0.7 mm
- It is the most popular material for flashings, such as roof flashings, windbreaks, gutter strips and eaves.
- Aluminum sheet:
- Thickness: 0.6 mm – 1.0 mm
- Aluminum is used where lightness and corrosion resistance are important, such as around areas exposed to moisture and salinity.
- Copper sheet:
- Thickness: 0.55 mm – 0.8 mm
- Mainly used in historic or exclusive construction, where appearance and durability are important.
- Titanium-zinc sheet:
- Thickness: 0.7 mm – 0.8 mm
- Often used in modern structures and on roofs with high aesthetic requirements.
- Stainless steel (inox):
- Thickness: 0.5 mm – 0.8 mm
- Used where high corrosion resistance and durability are important, such as in industrial facilities.
The choice of thickness depends on:
- Expected load (e.g., wind, snow).
- Type of construction and installation location.
- Aesthetics and durability of the material.
In practice, the most common thickness of flashings in residential construction is 0.5 mm for coated steel sheets.
Yes, our technical department provides full assistance in product selection, preparation and customization.
The coffers can be made in any RAL palette, in both matte and gloss varnishes.
The RAL color palette is an international color designation standard widely used in industry and construction. This system, developed in Germany in 1927, contains several thousand precisely defined colors, each of which is assigned a unique numerical code.
Powder coating of facade coffers is an advantageous solution for several important reasons:
- Durability and resilience
The coating obtained by the powder coating process is characterized by exceptional durability and resistance to a variety of factors:
- Mechanical damage
- Corrosion
- Weather conditions
- UV radiation
- Moisture
- Chemicals
As a result, facade coffers maintain their aesthetic appearance for a long time, up to 15-20 years6. This is especially important in the case of elements exposed to continuous exposure to external factors.
- Aesthetics
Powder coating makes it possible to obtain:
- Perfectly smooth and uniform surface
- Wide range of colors and finishes (matte, gloss, satin)
- Ability to create special effects, such as imitations of precious metals
Thus, facade coffers can be perfectly matched to the architectural design, enhancing the aesthetic value of the entire building.
- Ecology and economics
Powder coating is environmentally friendly:
- Does not contain solvents
- Does not emit harmful substances
- Allows reuse of excess powder
In addition, the process is economical due to the low consumption of material and the longevity of the resulting coating.
- Thermal and acoustic insulation
Powder-coated facade coffers help improve the thermal and acoustic insulation of a building, resulting in lower heating costs and greater comfort.
Steel facade coffers are used because of their many advantages, such as:
- The possibility of different perforation patterns.
- Long life and resistance to mechanical damage,
- Quick, easy and affordable assembly and disassembly,
- Excellent insulation of buildings against heating and heat loss,
- Modern design and harmonious connections thanks to invisible fasteners,
The process of installing aluminum and steel facade coffers begins with the preparation of the substructure, that is, the consoles and profiles that form the frame for the panels. Next, insulation, flashings around windows, doors and other elements, and ventilation grids are installed. Finally, the aluminum and steel facade panels are installed using horizontal fasteners and starter strips to provide stable support. Properly installed panels are resistant to weather conditions, including wind.
Yes, facade coffers can be part of a ventilated facade. They are one of the exterior finishing options in the ventilated facade system.
Façade coffers act as the exterior cladding in a ventilated façade system. They are mounted on a supporting structure that is anchored to the building wall. Such a structure makes it possible to create a ventilation gap between the cladding and the thermal insulation layer, which is a key element of a ventilated facade.
Ventilated facades are carefully designed building facades that consist of a metal frame and panels mounted on it. There is a ventilation gap between the wall and the facade, allowing air to flow freely, which cools the building during hot days. In addition, thermal insulation can be placed there to help keep the building warm in the colder months.
The cost of the training is 100 PLN + VAT. The condition for participation in training is payment of 100 PLN net + 23% VAT to the account PG Group
24 1090 2590 0000 0001 4505 5887 with an annotation:
“payment for participation in training on …”
with the exact date of the training. We will issue a prepayment invoice to the recorded payment and a final invoice after the training. The training is completed with the issuance of a Certificate authorizing the installation of our structures.
Training sessions are held at the company’s headquarters at the address below.
Please contact Customer Service to schedule a training date
Planned training time – 6 hours.
PG Group sp. z o.o.
Nowa Wieś Wrocławska
Relaksowa 41
55-080 Kąty Wrocławskie
- PG Group design discussion
- Discussion of free-standing structures divided into standard and bifacial structures, including:
- Types of construction by layout and size of PV modules
- Difference between the design for standard and bifacial panels
- Structures for photovoltaic farms
- Principles of construction assembly
- Discussion of construction for flat roofs with discussion of real cases including
- Selecting a structure for a flat roof
- Determination of wind zones within which structures can be installed
- Rules for determining installation zones and row spacing
- Technical aspects of flat roofs made of membrane in terms of construction of PV systems
- Can flat roofs be pitted?
- How to prepare a membrane roof for installation?
- Is welded construction better than ballasted construction?
- Can the welded structure withstand the wind load?
- How to install a welded structure on a flat roof made of membrane – discussion of installation of roof structures on flat roofs made of membrane
- Practical exercises of welding construction to PVC and bitumen membrane
The training will present all structural systems manufactured by PG Group, with a detailed discussion of flat roof systems, including welded, ballasted, east-west and south invasive systems.
Participants will be trained in the installation of PG Group structures, with emphasis on structures for flat roofs. The principles of installing PV structures on flat roofs made of membrane will be demonstrated, and practical exercises will be conducted to weld the membrane with a welding machine.