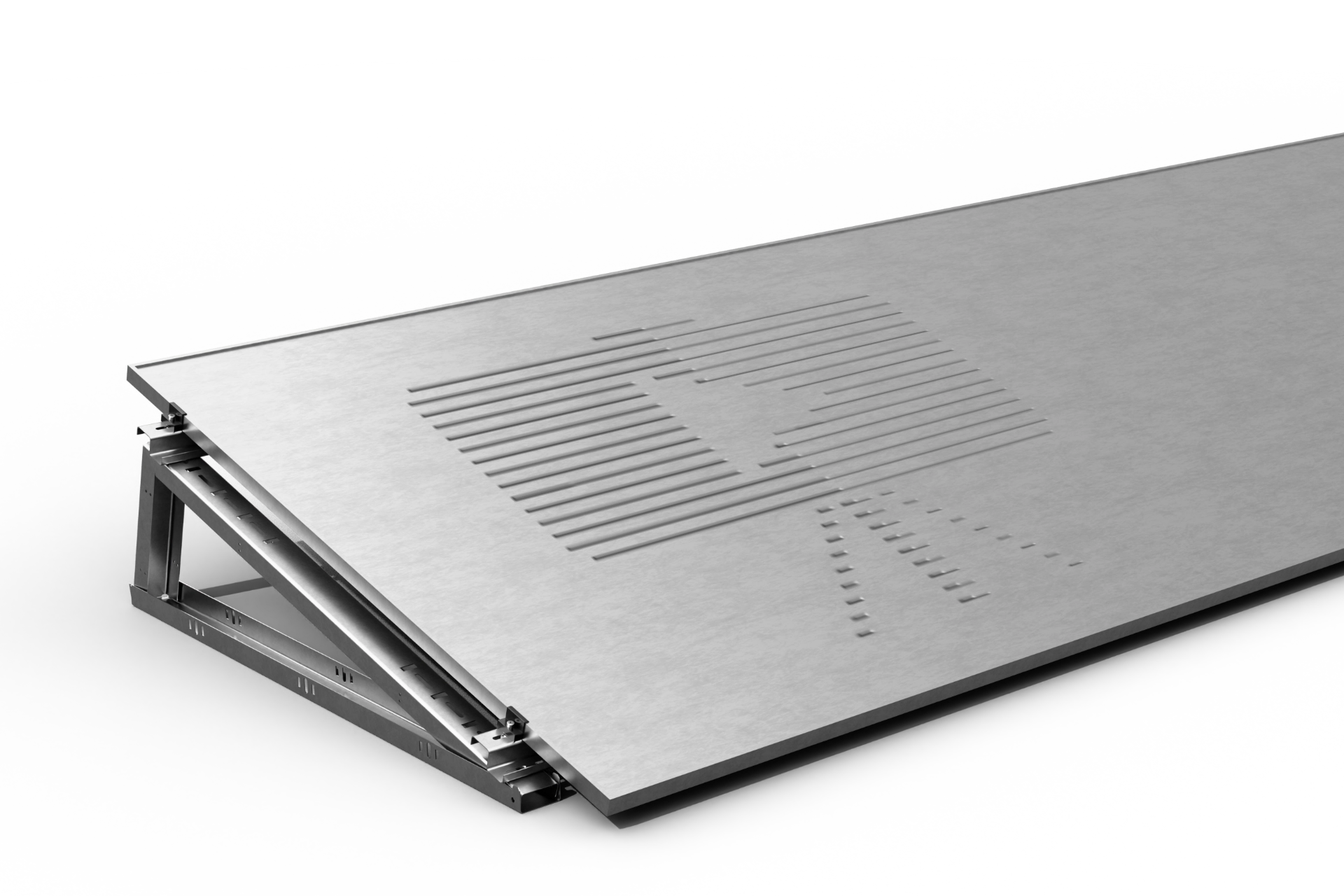
Training
Our training courses focus mainly on products. They include discussion of different variations and modifications, as well as assembly and installation techniques. We also encourage you to share your own ideas that we can adapt to your project. We conduct them in an open format! 🙂
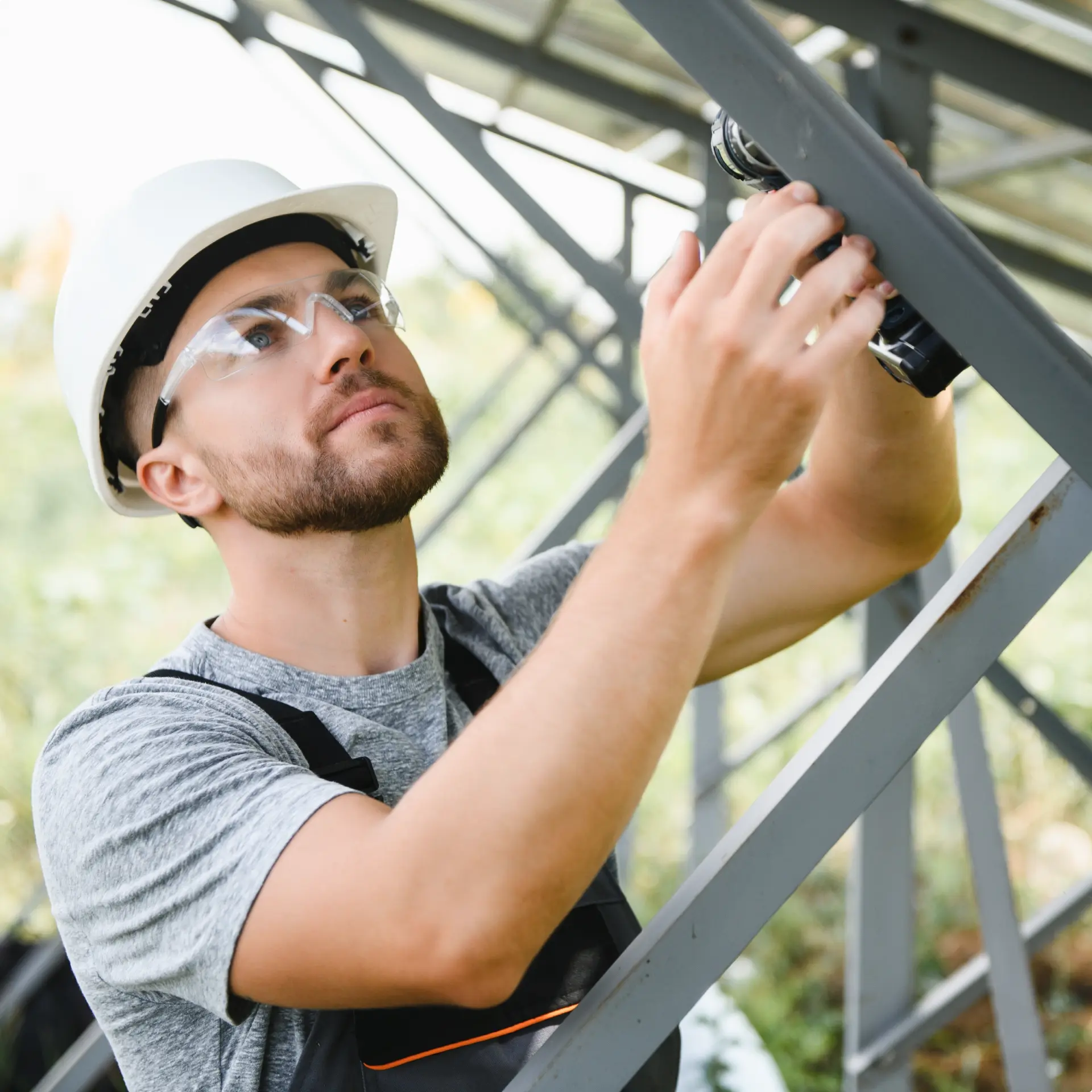
Flawless installation of mounting systems
We are committed to ensuring that the PV structures we manufacture are installed in a professional and proper manner. Therefore, the scope of training is always individually tailored to the needs and requirements of the customer and the project.
To facilitate the work of installers and fitters, we provide detailed training on the installation of each type of our structures. We discuss how to mount on different surfaces, define risks and compare nuances.
Benefits
You will learn about our products: their designs, types, variants and how to install them
The qualifications you acquire will guarantee that the terms of the guarantee will be upheld
You will receive a PG Group installer certificate, enjoy the best coffee and see our facility 🙂
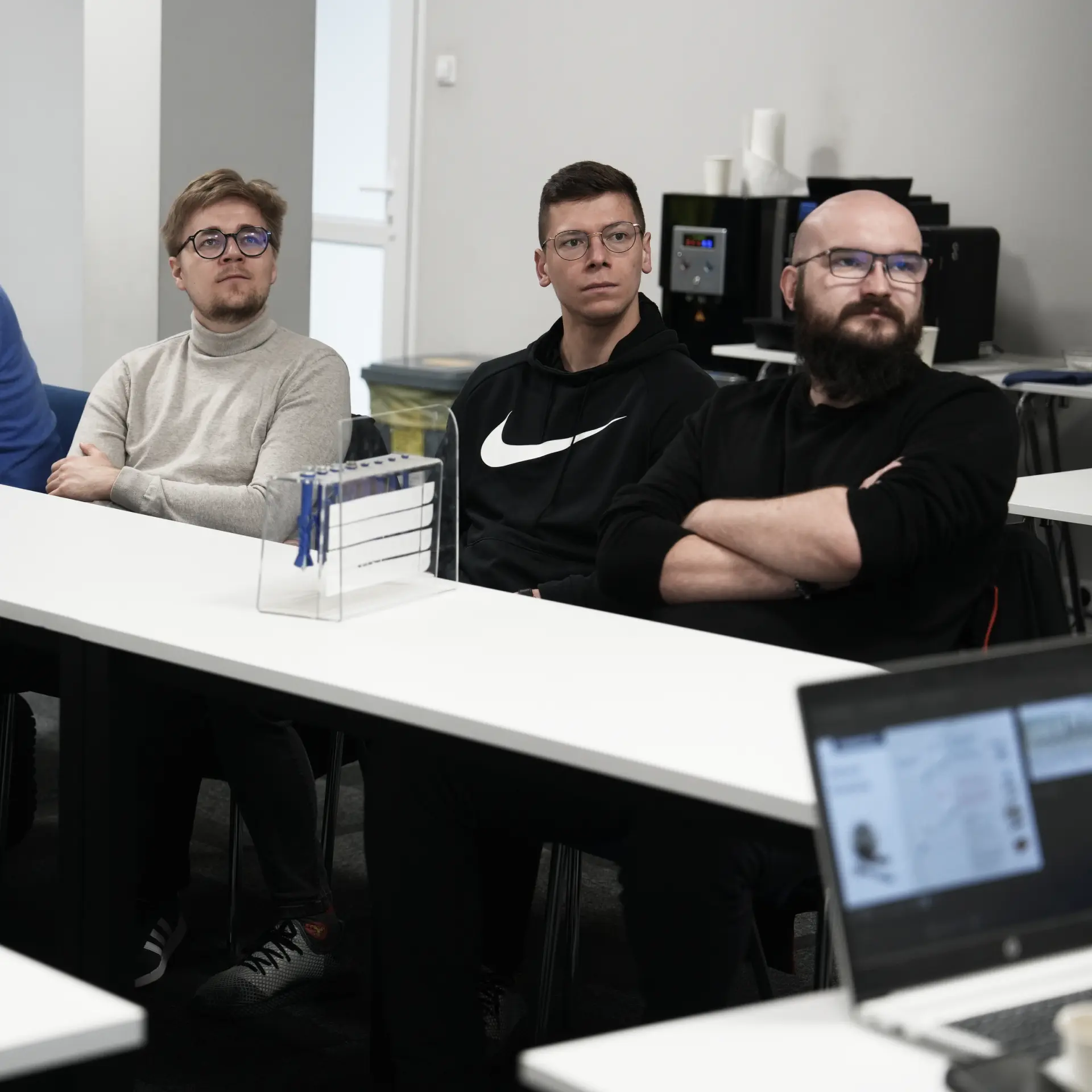
As a leading manufacturer of mounting systems, we are committed to complying with current building codes and standards. We keep abreast of current laws, but we also follow the latest industry trends. Accordingly, we ourselves regularly participate in the training of our business partners like Rawlplug (a leader in fasteners), and Protan (a leader in roofing).
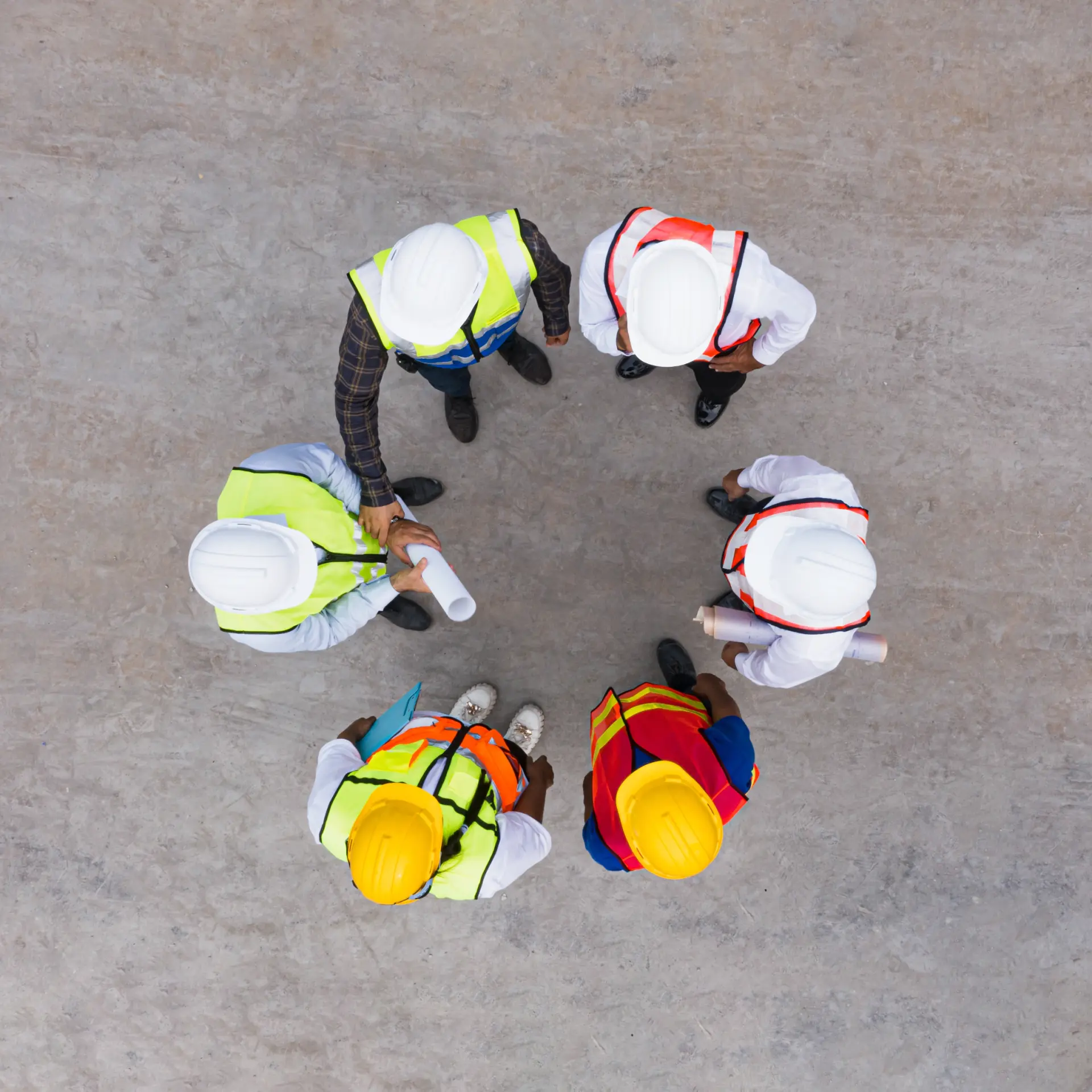
Czy na dachu płaskim lepiej stosować system inwazyjny czy nieinwazyjny? Jak bezpiecznie zamontować konstrukcję na grząskim gruncie? Czym różni się PosMAC, Granite® i Magnelis®?
PG Group has gone through all the steps needed to meet the ISO 14001 environmental standard and is certified. To obtain the ISO 14001 environmental standard, the company had to meet the following conditions:
Implementation of an Environmental Management System (EMS).
- Conduct a preliminary audit to assess the current state of the organization.
- Develop and implement a documented EMS system, including:
- Environmental policy
- System procedures
- Operational instructions
- Identification and evaluation of environmental aspects related to company operations.
- Identify environmental goals and objectives in line with company policy.
- Ensure compliance with applicable environmental laws and regulations.
Operation of the system
- Ensure management commitment to building and maintaining the EMS.
- Implement a process approach and PDCA (Plan-Do-Check-Act) cycle.
- Conduct monitoring and measurement of key environmental parameters.
- Training of employees on ISO 14001 requirements and implemented procedures.
- Implement operational controls for processes related to significant environmental aspects.
- Develop and implement emergency response procedures.
Certification
- Conduct an internal audit to verify compliance with the requirements of the standard.
- Take corrective and preventive actions when non-compliance is detected.
- Pass a certification audit conducted by an accredited certification body.
PG Group complies with EN 1090 and is certified The company had to go through the following stages:
Implementation of the Factory Production Control System (ZKP).
- Develop and implement a documented system of Factory Production Control (FPC).
- The ZKP system should cover all special processes used in production, such as:
- Design (if the company conducts such a process)
- Welding
- Corrosion protection
- Joining with mechanical fasteners
- Inspection and testing
- Provide adequate personnel, equipment and procedures to ensure product compliance.
Meeting technical requirements
- Meet the technical requirements of EN 1090-2 for steel structures or EN 1090-3 for aluminum structures.
- Conduct the first type test (ITT) and first type calculation (ITC) for products.
- Welding quality assurance according to ISO 3834 (part 2, 3 or 4).
Certification
- Passed initial inspection of factory production control by an accredited notified body.
- Successful completion of a certification audit covering the full scope of the ZKP system.
- Obtain a certificate for the Factory Production Control system and a Certificate for Welding.
Additional requirements
- Having qualified personnel, including welders with the appropriate licenses.
- Provide appropriate equipment for production, measurement and inspection.
- Implement a system for overseeing documentation and records.
- Development and application of product conformity assessment procedures.
The current EN 1090 certificate of conformity is valid until 12/12/2026.
Sheet metal perforation is the process of creating regular holes in metal sheets, which can have different shapes, sizes and patterns. These holes are usually arranged in a predetermined pattern (e.g., in rows, passing or otherwise). Perforation is performed to give sheet metal certain functional, aesthetic or technological properties.
Perforation features:
- Shape of holes: Round, square, rectangular, hexagonal, decorative (such as irregular patterns).
- Arrangement of holes: Regular (symmetrical) or irregular, in straight or staggered rows.
- Size of holes: From very small (e.g., less than 1 mm) to large (several centimeters).
- Degree of perforation: Percentage of perforated area in the total area of the sheet.
Sheet metal perforation methods:
- Mechanical (perforation press):
- The most widely used method in the industry, using dies and stamps.
- Laser:
- It allows precise cutting of any design, especially in custom production.
- Hydro cutting (hydro cutting):
- Used for complex shapes and materials that are difficult to work with.
- Chemical (digestion):
- Mainly used for thin sheets and delicate designs.
Applications of perforated metal sheets:
- Ventilation and permeability:
- In ventilation, air conditioning and filtration systems.
- Design and Architecture:
- Building facades, acoustic screens, suspended ceilings, balustrades, decorative elements.
- Industry and Technology:
- Screens in machines, guards, work platforms, acoustic panels.
- Protective applications:
- Security grating, machine guards, burglar protection.
- Agriculture and food industry:
- Machine components for sorting, drying or processing products.
Thanks to perforation, sheet metal can combine lightness with strength and functionality, making it an extremely versatile material.
In our offer we have welding services by various methods. Depending on the customer’s needs, we are able to offer welding by methods: TIG, MIG/MAG and electrode welding.
MaksyThe maximum thickness of laser cutting depends on the type of material:
- Stainless steel: 30 mm
- Carbon steel: 25 mm
- Aluminum: 25 mm
- Copper: 15 mm
These values are achievable on the TruLaser 3060, which offers the greatest cutting capabilities of the machines listed.
For sheet metal with a thickness of 2 mm, the maximum bending length is 8300 mm. This is possible on the VarioPress 300-80, which has a maximum bending length of 8300 mm and can handle materials up to 4.0 mm thick.
Galvanized sheet and zinc-magnesium coated sheet differ in several important features:
Coating composition
- Galvanized sheet: It is covered with a layer of pure zinc.
- Zinc-Magnesium Sheet: The coating consists of zinc with magnesium added, which provides better protective properties.
Corrosion resistance
- Galvanized sheet metal: Provides good protection against corrosion, but is susceptible to coating damage during transportation and installation.
- Zinc-magnesium sheet: It has much better corrosion resistance than galvanized sheet.
Durability
- Galvanized sheet: It has a shorter service life compared to zinc-magnesium sheet.
- Zinc-magnesium sheet: It is characterized by longer life and better protection of the steel substrate.
Thickness and weight of the coating
- Galvanized sheet metal: Requires a thicker coating for adequate protection.
- Zinc-Magnesium Sheet: Achieves comparable or better protective properties with less coating thickness and weight.
Resistance to weathering Zinc-magnesium sheet shows better resistance to salt spray, moisture and sulfur dioxide compared to galvanized sheet.
The completion date is determined by a number of factors, such as the complexity of the project, technological complexity, production volume and the current production plan of the plant. Each project is treated individually. The time can vary significantly and range from 1 to 4 weeks.
When it comes to the service business of our manufacturing plant in Nowa Wies Wroclawska, we focus on B2B cooperation. We cooperate with a wide range of companies from micro-enterprises to major global corporations. We do not have a set MOQ, but everything depends on the individual project.
Delivery time depends on whether it is an individual “tailor-made” project, or it is a standard order, the components of which are in stock. In the case of a standard design order, the time is limited only to the order reprocessing time and shipping time. For large individual projects, the lead time is usually several weeks, depending on the degree of preparation of the necessary information by the customer.